I. Introduction
A. The growing demand for private label washing powders
In recent years, the demand for private label washing powders has seen a significant increase. Consumers are looking for cost-effective alternatives to well-known brands without sacrificing performance or quality. Private label products offer a competitive edge in pricing and the opportunity for retailers to build their brand reputation.
B. The role of OEM services in the private label market
Original Equipment Manufacturer (OEM) services play a crucial role in the private label market. These service providers offer product development, manufacturing, and packaging solutions that help private label brands bring high-quality washing powders to the market.

C. The significance of quality control
Quality control is a critical aspect of OEM services, ensuring that private label washing powders meet customer expectations and adhere to industry standards and regulations. It builds trust and confidence in the brand and is essential for achieving long-term success.
II. OEM service overview
A. What is an OEM service?
OEM services refer to companies that manufacture products according to the specifications provided by another company. These manufacturers produce and package the products under the client’s brand name.
B. Benefits of OEM services for private label washing powder
OEM services offer several advantages for private label washing powder businesses, including:
- Access to experienced and skilled professionals
- Cost-effective production
- Streamlined supply chain
- Customization and flexibility
C. Identifying the right OEM partner
Choosing the right OEM partner involves evaluating factors such as:
- Technical expertise
- Quality control systems
- Manufacturing capabilities
- Communication and transparency
- Competitive pricing
III. Developing a tailor-made washing powder formula
A. Understanding customer requirements
To develop a successful washing powder formula, it is crucial to understand the target customers’ needs and preferences. This may involve conducting market research, analyzing customer feedback, and identifying market trends.
B. Customizing the formula based on the target market
Based on the customer requirements, OEM services should develop a customized formula that caters to the target market’s needs. This may include aspects such as fragrance, cleaning performance, eco-friendliness, and compatibility with various fabrics and washing machines.
C. Ensuring raw material quality and safety
Sourcing high-quality raw materials is critical for manufacturing a superior washing powder. OEM partners should have strict quality control measures in place to verify the safety and purity of raw materials, ensuring they meet industry standards and regulations.
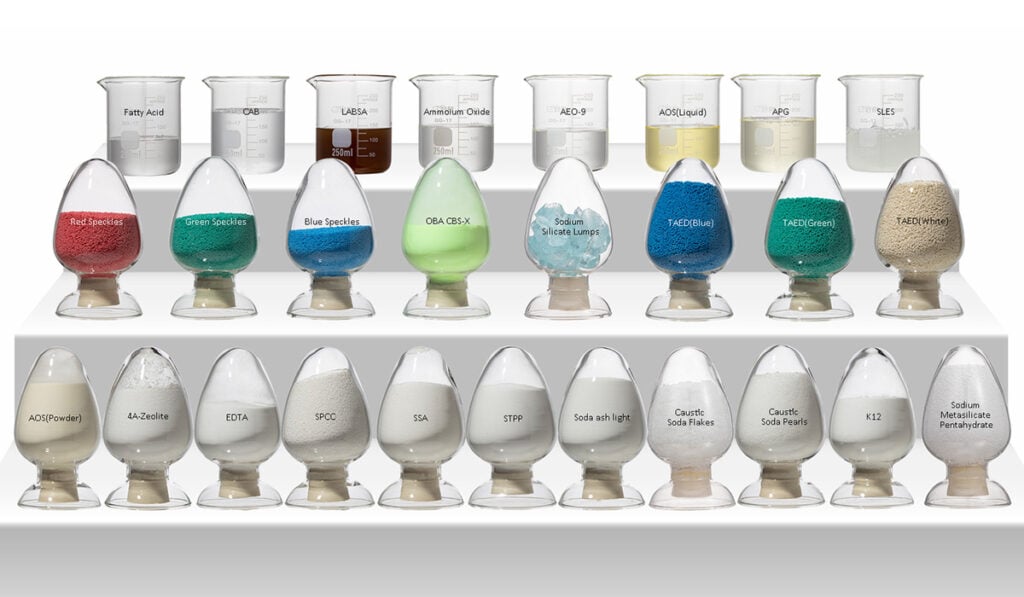
IV. Quality control at the raw material stage
A. Selecting reliable raw material suppliers
OEM services should work with reliable and reputable suppliers who can provide consistent quality raw materials. This involves evaluating supplier performance, conducting supplier audits, and verifying certifications and compliance with industry standards.
B. Inspecting raw material purity
Before using raw materials in the manufacturing process, OEM services must inspect their purity and quality. This may include conducting laboratory tests and verifying that materials meet predefined specifications.
C. Establishing strict raw material quality standards
OEM partners should establish strict quality standards for raw materials, ensuring that they meet or exceed industry regulations and customer expectations. This may involve defining acceptance criteria, developing inspection plans, and setting up quality control checkpoints.
V. Quality control during the production process
A. Implementing Good Manufacturing Practices (GMPs)
OEM services must adhere to Good Manufacturing Practices (GMPs) to ensure that the production process is consistent, efficient, and safe. GMPs involve maintaining a clean and hygienic production environment, regular equipment maintenance, and implementing standardized operating procedures.

B. In-process quality monitoring
OEM partners should monitor the quality of washing powder during the production process. Key aspects to monitor include:
- Batch consistency: Ensuring that each batch of washing powder has the same composition and quality.
- Particle size analysis: Verifying that the washing powder particles are of uniform size, contributing to consistent cleaning performance.
- Color uniformity: Ensuring that the washing powder has a consistent color, as it can impact the product’s overall appearance and marketability.
C. Addressing deviations and correcting errors
If deviations from the established quality standards are detected during the production process, OEM services should take immediate corrective action. This may involve adjusting equipment settings, replacing raw materials, or revising production methods.
VI. Final product quality control
A. Performance testing
Before the washing powder is released into the market, it should undergo performance testing to ensure it meets customer expectations. This includes:
- Cleaning efficiency tests: Evaluating the washing powder’s ability to remove dirt and grime from various fabrics.
- Stain removal tests: Assessing the product’s effectiveness in removing common stains such as oil, ink, and red wine.
- Compatibility tests: Verifying that the washing powder is compatible with different types of washing machines and fabric materials.
B. Physical and chemical property analysis
OEM services should also analyze the washing powder’s physical and chemical properties to ensure it meets industry standards. Key tests include:
- pH level measurement: Confirming that the washing powder has an appropriate pH level to prevent damage to fabrics and maintain cleaning efficiency.
- Moisture content assessment: Ensuring that the washing powder has a low moisture content, which helps prevent clumping and prolong shelf life
- Density analysis: Verifying that the washing powder has the correct density to ensure proper dosage and optimal cleaning performance.
C. Safety testing
It is essential to conduct safety testing to ensure that the washing powder does not pose any risks to consumers or the environment. These tests include:
- Skin irritation tests: Evaluating the product’s potential to cause skin irritation or allergies.
Environmental impact assessments: Assessing the washing powder’s biodegradability, impact on aquatic life, and overall environmental footprint.
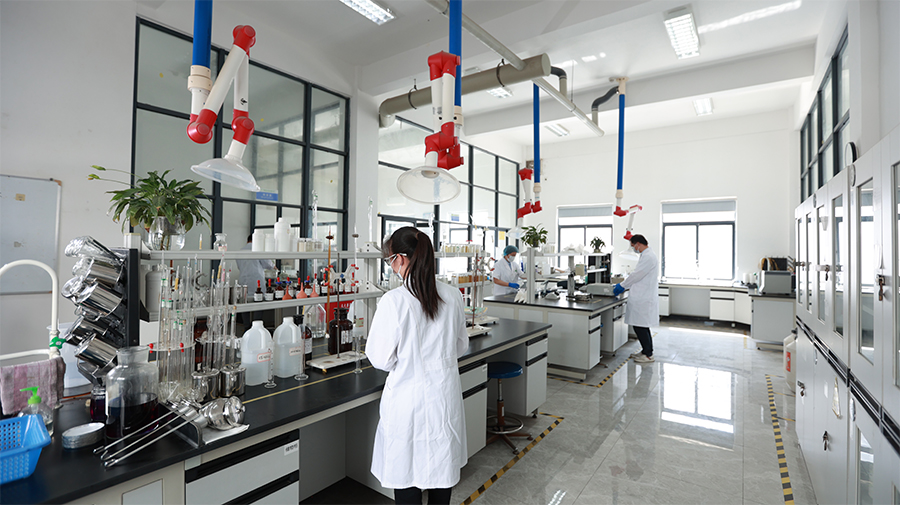
D. Packaging and labeling inspections
OEM services should inspect the packaging and labeling of the washing powder to ensure that it is accurate, informative, and compliant with industry regulations. This includes verifying the correctness of product information, usage instructions, and safety warnings.
VII. Quality management systems and certifications
A. Implementing ISO standards
OEM partners should implement internationally recognized quality management systems, such as ISO 9001, to demonstrate their commitment to quality control and continuous improvement.
B. Obtaining third-party certifications
Third-party certifications, such as eco-labels, can provide additional credibility and assurance of the washing powder’s quality and environmental performance. OEM services should strive to obtain relevant certifications to build trust with customers and clients.
C. Regular audits and continuous improvement
OEM partners should conduct regular internal and external audits to identify areas for improvement, ensure compliance with quality standards, and continuously enhance their quality control processes.
VIII. Traceability and transparency
A. Lot and batch tracking systems
Implementing lot and batch tracking systems can help OEM services maintain traceability throughout the supply chain, allowing them to identify and address any quality issues quickly and efficiently.
B. Sharing quality control data with clients
OEM partners should maintain open communication with their clients and share relevant quality control data to build trust and transparency. This may include sharing test results, inspection reports, and information about corrective actions taken in response to deviations.
C. Ensuring regulatory compliance
OEM services should stay up to date with industry regulations and ensure that their manufacturing processes and washing powders comply with all applicable standards and requirements.

IX. Handling customer feedback and complaints
A. Establishing a robust customer support system
OEM partners should have a robust customer support system in place to address any questions, concerns, or complaints from end-users or clients. This involves providing timely and accurate information and ensuring that any issues are resolved promptly.
B. Investigating and resolving product issues
In case of customer complaints, OEM services should thoroughly investigate the issue, identify the root cause, and implement corrective actions to prevent recurrence.
C. Utilizing feedback for continuous improvement
Customer feedback is a valuable source of information for improving the washing powder’s quality and performance. OEM partners should use this feedback to identify areas for improvement and implement changes to enhance the product.
X. Training and development of quality control personnel
A. Investing in employee training programs
OEM services should invest in employee training programs to ensure that their quality control personnel have the necessary skills and knowledge to perform their roles effectively.
B. Encouraging a quality-driven culture
Creating a quality-driven culture within the organization is vital for achieving excellence in quality control. This involves fostering a shared commitment to continuous improvement and maintaining high standards across all aspects of the business.
C. Retaining skilled and experienced professionals
Retaining skilled and experienced quality control professionals is essential for maintaining consistent product quality. OEM partners should offer competitive compensation packages and career development opportunities to attract and retain top talent.
XI. Conclusion
A. The significance of quality control in OEM services for private label washing powder
Quality control is a crucial aspect of OEM services for private label washing powder, as it ensures that the final product meets customer expectations, adheres to industry standards, and complies with regulations. Excellence in quality control is vital for building trust and confidence in your private label brand.
B. Building trust and confidence in your private label brand
By partnering with a reliable OEM service provider that prioritizes quality control, you can ensure that your private label washing powder consistently delivers excellent performance and value to your customers. This will help establish trust and confidence in your brand, leading to increased customer loyalty and long-term success.
C. Achieving long-term success through excellence in quality control
Maintaining a strong focus on quality control throughout the manufacturing process, from raw material sourcing to final product testing, is essential for achieving long-term success in the competitive private label washing powder market. By continuously improving your product quality and addressing customer feedback, you can stay ahead of the competition and grow your brand.
XII. Frequently Asked Questions
A. How can I ensure my OEM partner has adequate quality control measures in place?
Before selecting an OEM partner, conduct thorough research and ask for detailed information about their quality control systems, certifications, and past performance. You can also request references from their existing clients and conduct on-site audits to verify their quality control measures.
B. What should I look for in an OEM service provider for my private label washing powder?
Look for an OEM service provider with expertise in washing powder manufacturing, a strong commitment to quality control, transparent communication, competitive pricing, and a track record of meeting client requirements and industry standards.
C. How can I ensure my private label washing powder meets industry standards and regulations?
Partner with an OEM service provider that has a robust quality control system in place, adheres to Good Manufacturing Practices (GMPs), and complies with relevant industry standards and regulations. Additionally, stay informed about the latest industry requirements and work closely with your OEM partner to ensure that your washing powder consistently meets these standards.
D. Can I expect my OEM partner to handle all aspects of quality control, or should I be involved in the process?
While your OEM partner should handle most aspects of quality control, it is essential for you to maintain an active involvement in the process. This includes monitoring quality control data, conducting audits, providing feedback, and working closely with your OEM partner to address any issues or concerns.
E. How do I address customer concerns and complaints effectively while working with an OEM partner?
Establish a robust customer support system to address customer concerns and complaints promptly. Collaborate with your OEM partner to investigate and resolve product issues, implement corrective actions, and utilize customer feedback to continuously improve your washing powder’s quality and performance.